In diesem Fachartikel geht es um die besten Schweißmaschinen. Genauer gesagt, kann man im Voraus sagen, dass dieser Artikel sehr ausführlich ist, da alle konkreten Schweißgeräte und Schweißverfahren genauer beleuchtet werden und darüber hinaus ein grober Überblick geschaffen wird. Beginnen wir mit dem Werkstoff, der zu schweißen ist, der in der Regel auch als Werkstoff betrachtet und tituliert wird. Dazu kann man fast jeden bekannten Werkstoff nehmen, der von Natur aus metallischen Ursprüngen entstammt, sei es rein oder als Legierung. Natürlich verarbeitet man in der Regel zwei Werkstoffe, da Schweißen das Fügen von Werkstoffen beschreibt. Als Ausnahme gilt der sogenannte Plasmaschneider, der auch zum Schneiden oder Trennen von Metallen wunderbar geeignet ist und bei Einsätzen im Gebirge oft von Feuerwehr oder THW eingesetzt wird. Für das Verbinden, d.h. das Verschweißen dieser Materialien hat man nun die Qual der Wahl bei der Suche nach einem geeigneten Schweißgerät. Obwohl diese in der Regel unglaublich flexibel einsetzbar sind, bieten sie je nach zu verarbeitendem Material verschiedene Vor- und Nachteile. Dies sollte natürlich vor dem Kauf verschiedener Schweißgeräte berücksichtigt werden, um das für den Menschen am besten geeignete Gerät zu finden.
Um nur einige bekannte Schweißgeräte zu nennen, gibt es die oben erwähnten Plasmaschneider, MIG-MAG-Schweißgeräte, E-Hand-Schweißgeräte oder alle bekannten WIG-Schweißgeräte, die sicherlich für einen großen Teil der durchgeführten Schweißarbeiten verwendet werden. Natürlich gibt es noch viele andere Schweißgeräte, die jedoch weniger häufig vertreten und in der Regel auch sehr teuer im Betrieb zu halten sind. Sollte dennoch ein breiteres Interesse bestehen, finden Sie in weiterführenden Produkttests dieses Blogs nähere Informationen zu diesen. Nachdem nun sowohl der Werkstoff als auch die richtige Schweißmaschine gefunden sind, besteht zumindest die Hoffnung, dass wir uns nun den Zusatzstoffen zuwenden können. Schweißmaschinen arbeiten in der Regel mit einer Vielzahl von Zusatzstoffen, seien es die verschiedenen Gase, ob inert oder aktiv, die verschiedenen, zum Glück austauschbaren Elektroden oder die verschiedenen erhältlichen Extras, wie sie z.B. von der expondo GmbH im Internet angeboten werden. Natürlich gibt es für jedes Schweißgerät noch einige Zusatzmaterialien, seien es bestimmte Arbeitserleichterungen oder sicherheitsrelevante Dinge, wie Schweißhelm und entsprechende Handschuhe. Ein weiterer Aspekt, der bei allen Schweißgeräten und auch bei allen Schweißtechniken berücksichtigt werden sollte, sind die jeweiligen Sicherheitsbedingungen, die natürlich klar definiert und in den verschiedensten Normen festgelegt sind. Diese Vorschriften sind natürlich je nach Schweißmaschine recht unterschiedlich, sollten aber wegen der enormen Verletzungsgefahr beim Schweißen jederzeit angewendet werden. Im Großen und Ganzen wird viel über das Schweißen und die Schweißmaschine im Allgemeinen gesagt, wer das eine oder andere vertiefen möchte, ist in diesem Blog, wie bereits erwähnt, hervorragend lynotin.
Der Heißriss

Es ist der Schrecken eines jeden Schweißers, der eigentlich sehr schwer zu verhindern ist und in jedem Fall minimiert werden kann. In den meisten Fällen ist das Auftreten eines Heißrisses nicht auf die Schuld des Schweißers oder der Schweißmaschine zurückzuführen, sondern oft auf das Material, den sogenannten Werkstoff.Betrachtet man die Definition, so bezeichnet der Heißriss letztlich die durch das Schweißen verursachte Schädigung des Werkstoffs. Diese Verletzung tritt in der Regel während oder nach dem Erstarrungsprozess auf. Genauer gesagt geschieht dies zwischen der sogenannten Solidustemperatur und der Liquidustemperatur. Die Solidus-Temperatur ist die physikalische Größe, bei der ein Stoff in völlig fester Form vorliegt, während die Liquidus-Temperatur den Zustand beschreibt, in dem der Stoff aus einer Flüssigkeit zu erstarren beginnt. Der Heißriss entsteht also beim Übergang von einer Temperatur oder Phase zur anderen.Heißrisse sind in der Regel eher klein und dehnen sich sehr selten über eine Länge von mehr als einigen Millimetern aus. Im Wesentlichen handelt es sich bei Heißrissen im Wesentlichen um sogenannte Mikrorisse, die jedoch mit zerstörungsfreien Prüfverfahren nicht so leicht zu erkennen sind. Es liegt auf der Hand, dass man sich mit diesen nur dem möglichen Problem nähert, da das Werkstück einen gewissen Nutzen erhalten soll und deshalb möglichst nicht beschädigt werden soll.Da die verwendeten Materialien oft die Ursache von Heißrissen sind, ist es schwieriger, als man denkt, diese zu verhindern. Unabhängig davon, mit welcher Schweissmaschine minderwertige Werkstoffe verbunden werden, die entstehenden Temperaturen sorgen fast immer für die oben genannten Temperaturen und die daraus resultierenden Heiß-Kalt-Phasen. Ob ein Heißriss auftritt, liegt nicht an der Schweißmaschine oder ihrem Bediener.Es gibt heute eine große Anzahl guter Schweißgeräte, die sich im Laufe der Zeit immer weiter verbessert haben und auch in Zukunft weiter verbessern werden. Ob die kommenden Innovationen letztendlich eine Schweißmaschine erfinden werden, die das Auftreten von Heißrissen vollständig verhindert, bleibt fraglich. Erfahrene Schweißer entwickeln jedoch im Laufe der Zeit ein gewisses Gefühl für das Material, an dem Sie arbeiten, und können daher oft aufgrund ihrer Erfahrung schlechteres Metall erkennen und beim Schweißen eher auf das Material reagieren, was ebenfalls die Bildung von Heißrissen verringert, aber keinesfalls eine Garantie dafür sein kann.Bei den zu schweißenden Materialien handelt es sich meist um verschiedene Metallteile, wie z.B. Bleche, die in anderen Fertigungsverfahren hergestellt werden. Das Auftreten von Heißrissen bei der Weiterverarbeitung solcher Bleche deutet sicherlich auf die Qualität der Verarbeitung während der Produktion hin, was wiederum langfristig zu einer eigenständigen Erkundung auf dem Markt führen wird. Wer die am stärksten kontaminierten Metallteile verkauft, wird auf lange Sicht keine Kunden mehr haben, die diese mit einer Schweißmaschine bearbeiten würden. Diese Autoselektion führt auch zu einer Reduktion von Heißrissen an der späteren Schweißnaht.Als kleines historisches Beispiel für Materialfehler ist der unfertige Obelisk, der in Ägypten gefunden wurde und sich noch im Steinbruch befindet, leicht zu finden. Dieser würde heute der größte ägyptische Obelisk der Welt sein, wenn er tatsächlich irgendwo aufgestellt worden wäre. Da man damals keine moderne Ausrüstung hatte, sondern mühsam Stein auf Stein schlug, dauerte das Freilegen bis zur Entdeckung des Haarrisses sehr lange und viele Sklaven waren erschöpft. Umso trauriger ist sein Schicksal.
Die unterschiedlichen Schweißgeräte auf einen Blick
Das Zubehör
Plasmaschneider
Ein Plasmaschneider ist ein technisches Gerät, welches unter Zuhilfenahme eines Stahls aus Plasma Metalle zerschneidet. Plasma ist ein elektrisch leitfähiges Gas von einigen tausend Grad Celsius, welches vollständig aus freien Ladungsträgern wie Ionen und Elektronen besteht. Um Plasma zu erzeugen, sind hohe Energien und hohe Temperaturen notwendig. Diese hohen Energien und Temperaturen werden in einem Plasmaschneider durch einen Lichtbogen erzeugt. Das zu schneidende Metall wird bei diesen hohen Temperaturen natürlich flüssig und mithilfe von Druckluft von der Fuge weggeblasen. Um Oxidation zu vermeiden, werden bei einem Plasmaschneider oft auch Schutzgase eingesetzt.Die benötigte Energie für den Lichtbogen wird durch einen Inverter im Plasmaschneider zur Verfügung gestellt. Ein Inverter in einem Plasmaschneider erzeugt zunächst mit Hilfe eines Gleichrichters einen Gleichstrom. Dieser Gleichstrom wird danach wieder unter Zuhilfenahme speziell hergestellter Dioden und anderer elektronischer Bauteile mit einer Frequenz von 20 bis 150 Kilohertz zerhackt und mittels eines Transformators im Plasmaschneider in eine niedrige Spannung umgewandelt, die dann wiederum mittels Dioden und anderen Bauteilen gleichgerichtet wird, um dem Plasmaschneider die nötige Energie für den Lichtbogen zu Erzeugung des Plasmas zu liefern.
Gasflasche
Eine Gasflasche ist ein zumeist metallischer Behälter, der unter hohem Druck Gas in seiner flüssigen oder in einer stark komprimierten gasförmigen Form enthält. Eine Gasflasche kann unterschiedliche Volumina enthalten, meist aber nicht über 150 Liter. Der Druck in einer Gasflasche kann bis zu 300 bar betragen. Meist besteht eine Gasflasche aus hochwertigem Stahl, doch in jüngerer Zeit werden auch Flaschen aus Carbonfasern, Glasfaser oder Kunststoffen hergestellt.Zur Entnahme des Inhalts einer Gasflasche wird meist ein Druckminderer angebracht, der das gefahrlose Entnehmen des Gases aus der Gasflasche sicherstellen soll. Jede Gasflasche hat ihren Inhalt in ihrer Farbe codiert. Das für das autogene Schweißen benutzte Acetylen findet man in einer gelben Gasflasche. Der ebenfalls für diesen Zweck eingesetzte Sauerstoff befindet sich in einer blauen Gasflasche. Argon, das bei Schweißen als Schutzgas eingesetzt wird, wird in graue Flaschen abgefüllt. Auch unterscheiden sich die Gewinde an jeder Flasche je nach Art des Inhalts.
Die verschiedenen Schweißverfahren
Wenn Sie mit dem Schweißen beginnen und Ihre Arbeit tun wollen, brauchen Sie zunächst einmal Strom. Insbesondere beim Lichtbogenschweißen wird zur Erzeugung des hohen elektrischen Stroms eine externe Stromquelle verwendet. Die einfache Schweißstromquelle ist ein so genannter Schweißtransformator, in Form eines kurzschlussfesten Steuerfeldtransformators, der den Strom des aus der Muffe kommenden Wechselstroms erhöht und so das Schweißen ermöglicht. Die Schweissstromquelle ist daher ein sehr wichtiges Element beim Schweissen und kann durch die verschiedenen Transformatoren und Inverter so umgebaut werden, dass der für die Schweissmaschine benötigte Strom je nach Strom, Stromspannung und Stromart (Gleichspannung oder Wechselspannung) eingestellt wird. Für die Art der Spannung ist ein in den Geräten eingebauter Gleichrichter zuständig.
Da Gleichrichter die Aufgabe haben, aus Wechselspannung Gleichspannung zu erzeugen, d.h. die sogenannte Glättung durch Kondensatoren zu erreichen, fallen Gleichrichter in der Elektronik wie auch in der reinen Elektrotechnik neben anderen Wechselrichtern in eine Unterkategorie der allgemeinen Wechselrichter. Wie bereits angedeutet, werden für diese Verfahren sogenannte Schweißinverter eingesetzt, die letztlich nur eine Art Standard-Inverter sind und damit eine elektronische Schweißstromquelle darstellen. Da sie technisch ähnlich wie ein Schaltnetzteil arbeiten, kann auf ein Gerät namens Streufelderzeugung zur Wandlung verzichtet werden.
Das Inverterschweißen
Die durch den Schweißinverter erzeugte Schweißstromquelle wird bei fast allen Lichtbogenschweißverfahren, wie z.B. MIG-MAG oder WIG, eingesetzt. Invertergeräte sind so vielseitig wie möglich gebaut, so dass sie sowohl ein- als auch dreiphasig betrieben werden können. Wie bereits erwähnt, erfolgt die Glättung der Phasen der Wechselspannungskurven, wofür Leistungshalbleiter eine Art Zerhackung durchführen und diese dann mit kleinen Transformatoren auf eine relativ kleine Spannung herunterbrechen. Der Schweißstrom wird dann über Dioden entzerrt. Transformatoren sind von unterschiedlicher Größe, wobei nach der Faustregel gilt: je kleiner das Gerät, desto höher die Arbeitsfrequenz. Freunde der Mathematik würden in diesem Fall von umgekehrter Proportionalität sprechen. Daraus kann man also schliessen, dass die Schweissmaschine mit einem Schweisskanten-Inverter umso kleiner und einfacher gebaut werden kann, je höher die zu erreichende Frequenz ist. Die Vorteile der durch Inverter erzeugten Schweißstromquellen, die auch mit einem praktischen Nutzen verbunden sind, bieten nicht nur den erhöhten Wirkungsgrad, sondern auch die Möglichkeit, hochdynamische Schweißarbeiten wesentlich besser zu regeln.
Danach muss der Schweißstrom mit Hilfe geeigneter Dioden gerichtet werden. Die Grösse von Transformatoren gleicher Leistung ist etwa umgekehrt proportional zur Arbeitsfrequenz, d.h. je höher die Frequenz, desto kleiner und leichter kann der Transformator und die gesamte Schweissmaschine gebaut werden. Der Gesamtwirkungsgrad von Inverter-Schweißgeräten ist wesentlich besser als der von anderen Schweißstromquellen. Durch die erhöhte Arbeitsfrequenz lassen sich hochdynamische Schweißprozesse dann wesentlich besser regeln. Da Schweißgeräte vor allem auf Baustellen eingesetzt werden, wo man durchaus von der Abstinenz aller Stromanschlüsse ausgehen kann, ist die Schweißmöglichkeiten mit Hilfe von Generatoren, die von Verbrennungsmotoren angetrieben werden, eine fast unverzichtbare Option. Aufgrund der Größe der Generatoren, die für den Betrieb von Schweißgeräten erforderlich sind, werden diese nahezu immer von Dieselmotoren angetrieben. Der Nachteil ist die Geräuschentwicklung bei der Inbetriebnahme, die aufgrund des Verbrennungsmotors natürlich wesentlich höher ist als bei einem gleichwertigen elektronisch betriebenen Gerät.
Widerstandsstumpfschweißen
Es gibt zwei mehr oder weniger bekannte Methoden für das Widerstandsstumpfschweißen, nämlich das Pressstumpfschweißen und das Abbrennstumpfschweißen. Diese beiden Verfahren sind nicht nur leicht zu automatisieren, sondern auch vielfältig einsetzbar. Sie werden meist zum Verbinden von Rohrstrukturen, Rollen, Schienen-Beton-Verstärkungsstählen und Kettengliedern sowie zu Fensterrahmen, Schläuchen und Folien angewandt. Die Funktionsweise dieser Methode ist recht einfach und dem Widerstandspunktschweißen recht ähnlich. Die zu verwendenden Komponenten werden mit zwei Spannbacken gegeneinander gepresst und durch die angelegte elektrische Spannung an der Verbindungsstelle aufgeschmolzen. Auch die beiden Schweißverfahren sind sehr unterschiedlich. So wird beim Press-Stumpfschweißen die Spannung abgeschaltet, bevor die Bauteile zusammengedrückt werden, sodass sich im weiteren Verlauf eine entgratete, dicke Raupe bilden kann. Beim Abbrennstumpfschweißen hingegen werden die beiden Bauteile mit der benachbarten Spannung langsam angenähert und so in den entstehenden Kontaktbereichen unter deutlicher Zerstäubung aufgeschmolzen. Der entstehende Metalldampf bildet um die eigentliche Schweißstelle eine Schutzgasatmosphäre und reduziert bzw. verhindert so die Oxidation der geschmolzenen Legierung. Wie wir wissen, wird dieser Vorteil bei anderen Schweißverfahren mit Schutzgasen erzeugt. Um die Bildung eines Kurzschlusses zu verhindern, muss bei einem anhaltenden Schweißstromfluss genügend Material aufgeschmolzen werden, um die Oxidhäute aus der jeweiligen Fügezone zu entfernen. Darüber hinaus werden die Bauteile schneller aufeinander zu bewegt, wodurch das gesamte geschmolzene Material aus der Fügezone gedrückt wird. Der bei diesem Verfahren entstehende Grat an der Fügestelle, der beim Schweißen entsteht, muss natürlich anschließend entfernt werden, um eine saubere Schweißnaht zu erhalten.
Widerstandspunktschweißen
Dieses Schweißverfahren ist, wie der Name schon sagt, ein Widerstandsschweißverfahren zum nahtlosen Schweißen von Blechen. Dieses Punktschweißverfahren ist genauer in der RP, EN ISO 4063, beschrieben: Verfahren 21. Bei diesem Schweißverfahren werden die zu verbindenden Bleche durch zwei gegenüberliegende Elektroden an einem Punkt zusammengepresst und so miteinander verbunden. Da die Verschweißung zwischen den beiden Elektroden, d.h. an der Stelle des höchsten elektrischen Widerstandes, erfolgt, ist an diesem Punkt des Grundwerkstoffes auch der Schmelzpunkt. Dies geschieht deshalb so genau, weil der Widerstand an genau dieser Stelle etwa 30 Mal so hoch ist wie der des übrigen Materials. Das Zusammenführen der Schweißelektroden erfolgt in der Regel durch Zylinder oder eine Punktschweißzange. Die Elektroden, die aus Kupfer oder Legierungen wie Glidcop bestehen, werden durch Durchleiten von Kühlwasser vor Überhitzung geschützt. Die verwendeten Werkstoffe werden wegen ihrer günstigen Leitfähigkeit, aber auch aufgrund des im Verhältnis zum Werkstück relativ geringen Übergangswiderstandes für Wärme und Strom eingesetzt. Dieses Schweißverfahren, das vor allem in der Automobilindustrie zur Verbindung von Karosserieteilen eingesetzt wird, hat leider einen recht häufigen Fehlschluss, den so genannten Sekundärverschluss. Ein Grund hierfür kann eine Verringerung des Punktdurchmessers sein, bei dem die Wärmemenge zur Bildung der Schweißlinse durch das Ausströmen von Teilen des Schweißstroms über einen bereits geschweißten Punkt reduziert wird. Dies kann zum einen an der eigentlichen Vorrichtung zum Widerstandspunktschweißen liegen oder an der ungünstigen Konstruktion des Bauteils selbst. Eine Sonderform des Widerstandspunktschweissens ist das Bolzenschweissverfahren, das die vorgenannte Schweisstechnik mit Eigenschaften des Lichtbogenschweissverfahrens, wie es teilweise in WIG-Schweissgeräten eingesetzt wird, kombiniert. Bei diesem Schweißprozess werden Bolzen auf ein Blech oder einen massiven Körper aufgeschweißt, was in diesem Fall auch ohne Rückkontakt möglich ist. Dieses Verfahren ist nicht nur typisch für den Straßenbrückenbau, sondern wird auch für die kraftschlüssige Verbindung von Beton und Stahl sowie für das Schweißen von Ankerbolzen eingesetzt. Eine Methode, die als Alternative zum Punktschweissverfahren in Mode zu sein scheint, ist das so genannte Einpressen, mit dem man auch eine formschlüssige Umformung erreichen kann.
Rotations-Reibschweißen
Dieses Verfahren wird seit den 1970er Jahren auch in Deutschland eingesetzt und bietet durch die Kombination verschiedenster Werkstoffe einen exorbitanten Vorteil gegenüber anderen Schweißverfahren. Besonders hervorzuheben ist hier der Gewinn für die deutsche Automobilindustrie, in der z.B. Auslassventile für Verbrennungsmotoren mit diesem Verfahren in extrem kurzen Taktzeiten geschweißt werden können.
So werden z.B. hochwarmfester Stahl und härtbarer Stahl miteinander verbunden. Dieses spezielle Pressschweißverfahren funktioniert dadurch, dass die Energiezufuhr ausschließlich durch eine Relativbewegung der Fügeteile zueinander unter Druck eingeleitet wird. Voraussetzung für die Anwendung dieses Verfahrens ist, dass mindestens ein Fügeteil in der Fügezone eine rotationssymmetrische Form aufweist. Beim Rotationsreibschweißen wird dann ein Fügeteil gegenüber dem noch montierten zweiten Teil rotationssymmetrisch versetzt. Dieses Verfahren wird häufig beim Schweißen von Werkstoffen verschiedener Güteklassen eingesetzt, wie z.B. Rohrstangen und Verbinder oder auch Motorteile. Die Maschinen, die für diese Prozesse eingesetzt werden, ähneln in ihrem Aufbau den üblichen Drehmaschinen. Nach dem Funktionsprinzip enthalten sie in der Regel eine rotierende Spindel und ein nicht drehendes Gegenstück, das auf einem axial verschiebbaren Schlitten gelagert ist und gegen das rotierende Teil gepresst wird. Die jeweilige Axialkraft ist in etwa abhängig von den Dimensionen der jeweiligen Maschine, die von der Tischgröße bis zur Lokomotivengröße reichen können. Die resultierenden Kräfte können dann im Bereich von einigen 100N bis 10.000kN liegen, was einer Gewichtskraft von 1000t entspricht. Eine Variante des Reibschweißens ist die optionale Sonderanwendung des „positionierten Reibschweißens“, die allerdings noch eine spezielle Steuerung und einen speziellen Antriebsmotor erfordert.
Rührreibschweißen
Dieses Verfahren kann auch zum Schließen von oberflächlichen Poren und zur Verbesserung der Materialeigenschaften auf einer lokalen Oberfläche verwendet werden. Natürlich ist es bei der Vorstellung neuer, noch relativ unbekannter Verfahren immer wieder wichtig, Vor- und Nachteile zu erwähnen, so dass diese nun für die obige Schweißmaschine genannt werden.
Vorteile dieser Schweißmaschine
- Sie benötigen keine zusätzlichen Materialien
- Die erreichbare Nahtfestigkeit ist extrem hoch
- Die Verwendung von Inertgas ist nicht mehr notwendig
- Der Prozessablauf ist sehr einfach und daher nicht sehr fehleranfällig
- Die zu erreichenden Mischungen decken einen weiten Bereich von
- Relativ niedrige Schweißtemperaturen sind an der Schweißmaschine erforderlich, so dass der Verzug auf der Schweißoberfläche sehr gering ist
Nachteile dieser Schweißart
- Abhängig von der Bauteildicke und der Legierungsart liegen die Prozesskräfte zwischen einem und mehr als zwanzig Kilonewton und sind daher relativ hoch
- Der notwendige Kontakt von Schulter und Bauteil schränkt den 3D-fähigen Einsatz der Schweissmaschine ein
- Der Austritt des Werkzeugs am Ende der Schweissung erzeugt einen sogenannten Endkrater (Lösung ist ein automatisch zurückziehbarer Stift)
Die mit diesem Schweißverfahren arbeitende Schweißmaschine kann letztlich Blechteile aus verschiedenen Materialien mit einer Materialstärke von mehr als 30 mm umfassen, wobei die Schweißgeschwindigkeit und die erreichbare Einschweißtiefe, wie bei vielen anderen Schweißverfahren, nicht von der Schweißmaschine, sondern in der Regel von der Festigkeit und Härte des zu schweißenden Materials abhängt. Da die erforderlichen Prozesskräfte mit zunehmender Materialfestigkeit stark ansteigen, wird dieses Verfahren meist bei Aluminium und z.B. Metallschäumen eingesetzt (siehe Teil 1).
Das WIG-Schweißen
Anwendungen dieser Schweißgeräte
Da dieses Schweißverfahren vor allem zum Schweißen großflächiger Bauteile eingesetzt wird, handelt es sich bei den dafür verwendeten Schweißgeräten nicht um Schweißmaschinen in diesem Sinne, da es sich meist um Sondermaschinen handelt, die speziell auf die zu schweißenden Bauteile abgestimmt sind. Beim eigentlichen Schweißen kommen manchmal sogenannte Tricept Robotersysteme zum Einsatz, die durch ihre Automatisierung einen schnelleren und sicherlich flexibleren Arbeitseinsatz ermöglichen. Wie bereits erwähnt, erfreut sich diese Art von Schweißmaschinen vor allem in der Flugzeugindustrie, im Schiffbau, im Schienenfahrzeugbau und sogar in der Weltraumfahrt zunehmender Beliebtheit, und auch die Automobilindustrie sollte nicht unerwähnt bleiben, insbesondere in Deutschland. Schließlich ist noch eine Hybridvariante des Rührreibschweißens zu erwähnen, nämlich das LAFSW-Schweißen. Hier wird die Schweißmaschine durch eine zusätzliche Laserstrahlleiter unterstützt. Natürlich wird der eigentliche Schweißprozess durch diese Unterstützung erleichtert, was zu einer höheren Schweißgeschwindigkeit als bei der ursprünglichen Schweißmaschine führt. Es sollte nur klar sein, dass der Einsatz eines Lasers mit einem zusätzlichen Energieaufwand verbunden ist, der den bereits erwähnten Nachteil der hohen Prozesskräfte bei dieser Schweißmaschine verstärkt.
Gängige Probleme
Beim Schweißen passieren schnell Fehler, die zu unbeabsichtigt unansehnlichen Ergebnissen führen. Um die möglichen Probleme zu vermeiden, ist es wichtig, die Fehler und ihre Ursachen zu kennen.Aus diesem Grund wollen wir einige häufige Fehler beleuchten.
Die Einbrennkerbe:
Wenn die Schweißnaht auch in das Bauteil eindringt und das Bauteil dadurch beschädigt wird, spricht man von einer Einbrennkerbe.Die häufigsten Ursachen für diesen Fehler sind zum einen eine zu steile Elektrodenhaltung oder zum anderen die Wahl eines zu langen Lichtbogens.
Der letzte Krater
Dabei entstehen an der Schweißnaht sogenannte Schrumpfrisse. Diese entstehen, wenn die Schweißnaht zu schnell abkühlt.Der Grund dafür ist das zu schnelle Entfernen der Schweißmaschinenelektrode aus der Schweißnaht am Ende.
Schlackeneinschlüsse
Schlackeneinschlüsse sind ein Indiz dafür, dass Sie entweder mit zu wenig Strom arbeiten und ihn deshalb erhöhen sollten, oder dass Sie mit zu hoher Geschwindigkeit schweißen.In der Ruhe liegt die Kraft!
Gaseinschlüsse
Gaseinschlüsse oder Poren zeugen in der Regel davon, dass die Werkstückoberfläche unsauber ist. Das heißt, auf Ihrer ist wahrscheinlich Rost, Fett oder eine Beschichtung.Wenn dies nicht der Fall ist, kann das Auftreten von Poren auch auf die Wahl eines zu langen Bogens hinweisen.
Risse im Schweißnahtübergang
Wenn zwei Komponenten miteinander verschweißt werden, können Risse zwischen den Teilen entstehen. Dies ist oft ein Zeichen dafür, dass das Material nicht zum Schweißen geeignet ist.Manchmal kann aber auch eine zu niedrige Umgebungstemperatur vorliegen, so dass die Werkstücke zu schnell abkühlen und dadurch Risse bilden.
Der Wurzeldefekt
Ein Wurzelfehler tritt auch direkt am Übergang zwischen den Komponenten auf. In diesen Bereich gelangt Schlacke.Der Grund dafür liegt meist in einem zu grossen Stirnabstand.
Natürlich wird der eigentliche Schweißprozess durch diese Unterstützung erleichtert, was zu einer höheren Schweißgeschwindigkeit als bei der ursprünglichen Schweißmaschine führt. Es sollte nur klar sein, dass der Einsatz eines Lasers mit einem zusätzlichen Energieaufwand verbunden ist, der den bereits erwähnten Nachteil der hohen Prozesskräfte bei dieser Schweißmaschine verstärkt.
Autogenschweißgerät
In einem Autogen-Schweißgerät wird das zu schweißende Metall durch Verbrennungsgase erhitzt. In diesem Fall wird in der Regel ein Gemisch aus Sauerstoff und Acetylen, dessen genaue chemische Bezeichnung Ethin lautet, verbrannt. Dadurch wird ein Metallstab, der Schweißdraht, geschmolzen, und diese Schmelze kann zum Verbinden von Metallwerkstücken verwendet werden. Wenn das Selbstschweißgerät als Schweißbrenner verwendet wird, wird die Flamme der Flamme von zusätzlichem Sauerstoff hinzugefügt. Dadurch wird das geschmolzene Metall zu Schlacke oxidiert und durch den Gasdruck der Flamme weggeblasen. Ein Auto-Schweißgerät hat austauschbare Brennstoffdüsen. Folglich kann ein einziges automatisches Schweißgerät für viele verschiedene Materialien und Materialstärken verwendet werden. Die Autogen-Schweißmaschine hat zwei Regler im Handgriff, mit denen die Zufuhr von Acetylen und Sauerstoff geregelt wird. An der Rückseite befinden sich Anschlüsse für die Schläuche, die zu den Gasflaschen mit Acetylen und Sauerstoff führen. Um Verwechslungen zu vermeiden, sind die Schläuche in einem Autogenschweißgerät unterschiedlich eingefärbt. Hier hat der Schlauch, der den Sauerstoff zum Brenner führt, ein blau gefärbtes Rohr, während das Acetylen durch einen rot gefärbten Schlauch zur Verbrennung geführt wird. Auch die Gewinde sind unterschiedlich, so dass es nicht möglich ist, die beiden Schläuche an der Autoschweißmaschine zu wechseln.
Schweißgeräte und Arbeitsschutz
Wie in jedem Arbeitsbereich müssen Sie auch beim Schweißen eine Menge Sicherheitsbestimmungen beachten, unabhängig davon, welche Schweißmaschinen Sie verwenden. Natürlich gibt es bestimmte Vorgaben, die je nach verwendeter Schweißausrüstung variieren können, gleichzeitig sind aber auch verschiedene allgemeine Vorschriften zu beachten. Beim Schweißen ist man in der Regel starken Strömungen, explosiven Verbindungen sowie toxischen Gasen ausgesetzt, die während des Schweißprozesses entstehen, und es besteht auch eine Gefährdung des eigentlichen Werkstoffes, z.B. durch Versprühen des heißen, meist flüssigen Metalls. Mit dem eingesetzten Schweißgerät ändern sich auch die Belastungen und die jeweils erreichte Intensität der Gefahrstoffe, wie z.B. die Toxizität, die sich bei Verwendung von Nickelverbindungen als Schweißzusatz in Form von Bronchitis äußern kann. Die Bildung toxischer Gase ist ein großes Problem, da in den meisten Fällen keine geeigneten Absaugvorrichtungen zum Schutz des Schweißpersonals installiert sind, wie sie beim Einsatz verschiedener Schweißgeräte notwendig sind. Dennoch ist für die Kontrolle der Lunge von Schweißern eine regelmäßige Rotation gemäß der Sondergesundheitsvorschrift G39 erforderlich, um dieser besonderen Gefahr langfristig Rechnung zu tragen. Wie immer ist in Deutschland der Umgang mit diesen Stoffen besonders geregelt, zum einen sind so genannte TRK-Grenzwerte einzuhalten, zum anderen ist die Einrichtung von Arbeitsplätzen, an denen Schweißgeräte regelmäßig eingesetzt werden, wiederum in der TRGS 528 geregelt. In der Regel wird bei der Einrichtung eines Arbeitsplatzes zum Schweißen eine Gefährdungsbeurteilung durchgeführt, bei der die Inhaltsstoffe der Schweißgase, die in Abhängigkeit von den verwendeten Werkstoffen entstehen, sorgfältig berücksichtigt werden können und somit der höchstmögliche Schutz in der Folgezeit durch gezielte Einstellungen und Anpassungen entsprechend der Schweißausrüstung gewährleistet werden kann. Natürlich ist nicht nur der richtig gestaltete Arbeitsplatz wichtig, um ein höchstmögliches Maß an Sicherheit für die Mitarbeiter, die die Schweißgeräte bedienen, zu gewährleisten, sondern auch eine nachhaltige Schulung und Unterweisung der Bediener für die jeweiligen Schweißgeräte sowie deren Vertiefung in regelmäßigen Abständen. Die richtige Unterweisung wird im Arbeitsschutzgesetz erneut gefordert und ist daher in jedem Betrieb zwingend durchzuführen. Auch ein Ausbildungsnachweis, der nach Möglichkeit vom Schweißer durchgeführt werden kann, ist in den meisten Branchen, die mit Schweißgeräten arbeiten, üblich. Die letzte Instanz in diesem Beruf ist die so genannte Schweißaufsicht, auf die in diesem Blog bereits gesondert eingegangen wurde. Seitdem sind wir bei der Schweißaufsicht gelandet, die ihre Daseinsberechtigung in jedem größeren Unternehmen aufgrund einer Vielzahl von Normen hat, die sowohl national als auch international klar definiert sind. Wer mehr über dieses Thema, das Aufgabengebiet und die gezielte Ausbildung einer Schweißaufsicht erfahren möchte, findet es im Artikel „“Schweißtechnische Ausbildung““, in der Rubrik Allgemeines. Um das volle Gefahrenpotential auszuschöpfen und vielleicht die eine oder andere Massnahme zu spezifizieren, werden nun die verschiedensten Schweissverfahren, die mit den jeweiligen Schweissgeräten durchgeführt werden können, angesprochen.
Autogenes Schweißen:
Funkenbildung ist möglich, was bedeutet, dass eine Schutzbrille getragen werden muss, um die Augen vor Funken oder glühenden Teilen zu schützen. (empfohlene Schutzklasse 2 bis 8)
Lichtbogenschweißen:
Lichtbogenschweißen wird in vielen Schweißgeräten eingesetzt, z.B. in mig MAG-Schweißgeräten oder WIG-Schweißgeräten, die eine Vielzahl von Schweißgeräten den Gefahren aussetzen, die gerade hier auftreten. Bei der Verwendung dieser Schweißgeräte muss vor allem die Herkunft der beiden schädlichen Strahlungsarten, nämlich der ultravioletten Strahlung und der Infrarotstrahlung, berücksichtigt werden. Um sich ausreichend zu schützen, werden Schutzbrillen mit entsprechenden Schutzklassen nach EN 169 empfohlen. Da UV-Strahlung auch die Haut angreift, wird in der Regel ohnehin ein Schwitzhelm getragen, der das Gesicht zusätzlich schützt. Moderne Schweißhelme verfügen über einen automatisch regulierenden Schweißer-Schutzfilter und passen sich so der geforderten Schutzklasse an. (empfohlene Schutzklasse 9 bis 16)
Laserschweißen:
Da Schweißgeräte zum Laserschweißen in der Regel fest installiert und damit sicher umschlossen sind, z.B. durch Laserschutzfenster und geeignete Schutztüren, werden mögliche Verbrennungen auf der Netzhaut und auch auf der Hautoberfläche durch direkte Strahlung oder Streustrahlung minimiert. Der Laser, der bei dieser Schweißmaschine eine zusätzliche Gefahrenquelle darstellt, wird beleuchtet und kann nur durch angepasste Laserschutzkleidung minimiert werden. Selbstverständlich sind auch geräteunabhängige Schutzmaßnahmen zu beachten. Empfehlenswert ist die Kleidung des Schweißers, die auf jeden Fall schwer entflammbar sein und alle Hautflächen bedecken sollte, um Strahlungsschäden zu vermeiden, sowie ein geeigneter Gehörschutz, der für die meist sehr lauten Geräusche, die je nach Schweißgerät zu unterscheiden sind, geeignet ist. Die bereits im vorigen Artikel erwähnten Gefahren durch entstehende Staubpartikel werden durch die dort beschriebenen Maßnahmen teilweise abgedeckt, ferner kann man der persönlichen Schutzausrüstung einen Gebläsefilter hinzufügen, der in Räumen mit ausreichender Belüftung sinnvoll ist. Wenn Sie mit einer Schweißmaschine in Räumen ohne Frischluftzufuhr arbeiten, sollten Sie ein luftunabhängiges Atemschutzgerät tragen. Ein weiterer zu berücksichtigender Aspekt ist die im Merkblatt der BGI 553 vorgeschlagene Vorsichtsmaßnahme zu deren Schutz bei Arbeiten in elektrisch leitfähigen Räumen, da von den meisten Schweißgeräten auch eine elektrische Gefährdung ausgeht. Schließlich ist es notwendig, den Schutz der Anwohner zu gewährleisten, was letztlich auch die Reduzierung von Strahlung und Lärm erfordert. Dies kann heutzutage durch verschiedene Systeme erreicht werden, wie z.B. sogenannte Schweißervorhänge, Schweißerlamellen oder große Schallschutz-Trennwandsysteme. Wenn man ehrlich ist, sieht man solche aufwendigen Schutzmaßnahmen sporadisch, wenn überhaupt nur bei langjährigen Großbaustellen. Sollten noch Fragen offen sein, werden die zuständigen Verbände sicher eine Antwort finden. Die Verbände sind in Deutschland durch den DVS, europaweit durch die EWF und weltweit durch die Institution des IIW vertreten.
Auftretende Gefahren beim Schweißen
Um den höchstmöglichen Schutz für die mit Schweißgeräten arbeitenden Mitarbeiter zu gewährleisten, wird für jeden Schweißarbeitsplatz zunächst eine Gefährdungsbeurteilung durchgeführt, bei der alle im möglichen Schweißrauch enthaltenen Bestandteile wie Titandioxid, Fluoride, Eisenoxide und Magnesiumoxide sowie Legierungsbestandteile wie Kobalt, Nickel, Chrom und Mangan berücksichtigt werden. Einige Stofffreisetzungen, wie z.B. die von Chromaten, können durch den Einsatz oder die Vermeidung bestimmter Schweißtechnologien reduziert oder vermieden werden. Dies gilt für jedes Schutzgasschweißen oder automatisierte Schweißen, bei dem keine freiliegende Elektrode verwendet wird. Neben der Untersuchung des Arbeitsplatzes wird natürlich auch die dort zu beschäftigende Person eingehend untersucht. Auf diese Weise werden alle Mitarbeiter unterwiesen, was nach dem Arbeitsschutzgesetz obligatorisch ist, die ihrerseits ihre Fähigkeiten durch einen Ausbildungsnachweis, z.B. einen Facharbeiterbrief, bescheinigen müssen. Je nach Umfang oder Komplexität der Arbeitsaufträge werden in vielen Industriezweigen Schweißaufsichtspersonen (EN ISO 14731) benötigt.
Bei autogenen Schweißprozessen ist aufgrund des möglichen Funkenfluges ein angepasster Augenschutz erforderlich. Die dafür erforderlichen Schutzbrillen sind ebenfalls eingefärbt, um blendfreies Arbeiten zu ermöglichen. Die durch die Gläser erzielte Abschirmung muss natürlich auch vor Ultraviolett- und Infrarotstrahlung schützen, wie es z.B. beim Lichtbogenschweißen der Fall ist. Je nach Strahlungsintensität werden die Schutzgläser in Schutzklassen eingeteilt, die in der Euronorm EN 169 definiert sind. Um die verschiedenen Strahlungen gemeinsam abzuschirmen, werden heute meist automatisch regulierende Gläser eingesetzt.
Um einen weiteren Schutzaspekt zu erfüllen, werden die oben genannten Brillen meist in Helmen eingesetzt, die ohnehin getragen werden sollten, um die Gesichtshaut z.B. vor UV-Strahlung zu schützen. Dieses Gesamtpaket gibt es entweder als eine Art Haltemaske, die eine Hand blockiert und damit den Bewegungsspielraum einschränkt, oder als Schutzhelmlösung, bei der dann aber beide Hände frei sind und zur Arbeit benutzt werden können. Dieses Schweißzubehör wird im Allgemeinen einfach als Schweißerhelm bezeichnet und gehört heute zu jedem Schweißer. In diesen kann auch ein eventueller Gehörschutz integriert werden, da dieser aufgrund der Lärmentwicklung bei bestimmten Schweißverfahren ebenfalls zu empfehlen ist. Neben dem Helm sollte natürlich auch der übrige Körper geschützt werden, wozu natürlich auch Sicherheitsschuhe sowie feuerfeste Schweißerkleidung gehören sollten. Die für den Schutz von Staubpartikeln notwendigen Absaugsysteme können entweder durch mobile oder stationäre Schweißrauchfilter eingesetzt werden. Ist eine solche Vorrichtung nicht installiert, muss der Schweißer seiner persönlichen Schutzausrüstung einen Gebläsefilter (PAPR) beifügen. Werden Schweißarbeiten in engen, luftarmen Räumen, wie z.B. Schächten oder z.B. Rohren, durchgeführt, muss zusätzlich ein Atemschutzgerät getragen werden, da durch das Schweißen zusätzlicher Sauerstoffmangel entstehen kann. Wichtig ist natürlich auch der Schutz aller Personen in der unmittelbaren Umgebung, die logischerweise auch vor Lärm und Strahlung geschützt werden müssen. Um einen optimalen Schutz gegen die beim Schweißen auftretenden normalen Risiken zu gewährleisten, können Schweißrippen, Schweißvorhänge oder auch Schweißerschutz-Trennwandsysteme eingesetzt werden. Elektrische Gefährdungen, wie sie beim Lichtbogenschweißen auftreten, sind natürlich eine große Gefahr für die Anwesenden, insbesondere in elektrisch leitfähigen Räumen. Abhilfe schafft hier unter anderem die Berufsgenossenschaft Metall mit dem Merkblatt BGI 553, in dem diese Problematik aufgegriffen wird. Nur das Laserschweißen als solches garantiert noch eine direkte Gefahr, da der verwendete Laserstrahl in der Regel unsichtbar ist, seine Länge aber nicht offensichtlich begrenzt ist. So kann ein falsch ausgestrahlter Laser oder die dabei auftretende Streustrahlung zu oberflächlichen Verbrennungen und im schlimmsten Fall auch zu Netzhautverletzungen führen. Um dies zu vermeiden, werden Laserschweißgeräte in den meisten Fällen sicher gelagert oder hinter entsprechendem Schutzglas oder Metall aufbewahrt. Verbände, die diese Probleme systematisch untersuchen und zu einer gemeinnützigen Lösung bringen, sind der DVS in Deutschland, die EWF auf europäischer Ebene und das IIW weltweit. Diese Verbände sorgen auch für die internationale Zusammenarbeit, z.B. bei der Ausbildung, den nachfolgenden Zertifizierungen und Normungen sowie der technisch-wissenschaftlichen Weiterentwicklung auf dem Gebiet der Schweiß- und Fügetechnik.
Das Schweißen
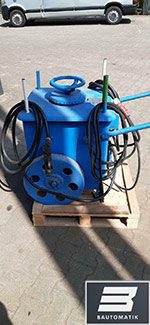
Das Wolframschutzgasschweißen wurde in den Vereinigten Staaten um 1936 als Argonac-Schweißen bekannt und breitete sich erst viel später, 1950, nach Europa aus. In allen angelsächsischen Ländern wird das WIG zu WIG, was natürlich auf die englische Bezeichnung Tungsten für Wolfram zurückzuführen ist.
Vorteile
Ein Vorteil von vielen, die das WIG-Schweissverfahren mit sich bringt, ist die Möglichkeit, so gut wie jedes für das Schmelzschweissen geeignete Material hinzuzufügen. Bei diesem Schweißverfahren entstehen praktisch keine Schweißspritzer und der entstehende Schweißrauch ist relativ gering. Darüber hinaus wird keine abschmelzende Elektrode verwendet. Aus diesem Grund ist die Zugabe von Schweißzusätzen vom Strom entkoppelt. Dadurch kann der Schweißer den zu verwendenden Heizstrom optimal auf seine Aufgabe abstimmen und die jeweiligen Schweißzusätze genau einstellen. Aus diesem Grund eignet sich das WIG-Schweißverfahren besonders zum Schweißen von Wurzellagen und in Zwangslagen. Die relativ geringe Wärmeeinbringung führt kaum zu Schweißverzug der Werkstücke und damit zu einer hohen Schweißqualität. Um dies zu erreichen, muss man allerdings eine relativ geringere Schweißgeschwindigkeit in Kauf nehmen, erreicht aber eine höhere Qualität. Dies wird für verschiedene Anwendungen, wie z.B. für den Rohrleitungs- und Apparatebau, aber auch für Kraftwerke und die chemische Industrie, als besonders wichtig und deshalb notwendig erachtet.
Gebäude
Ein WIG-Schweißgerät besteht in der Regel aus einer Energiequelle, die sowohl mit Gleichstrom als auch mit Wechselstrom betrieben werden kann und einem Schweißbrenner, der an ein Schlauchpaket angeschlossen ist. Im Schlauchpaket befinden sich neben der Schweißstromleitung die Steuerleitung, die Steuerleitung, die Schutzgaszufuhr und bei größeren Brennern manchmal auch die Installation von Kühlwasservor- und -rücklauf. Die Zündung des erforderlichen Lichtbogens kann ebenfalls auf zwei verschiedene Arten erfolgen, nämlich durch Kontakt- oder durch Hochfrequenzzündung. Als Gas werden in der Regel Edelgase wie Argon und/oder Helium verwendet (dies ist auf das erforderliche träge Ansprechverhalten zurückzuführen). Helium ist hier teurer, erhöht aber aufgrund seiner besseren Wärmeleitfähigkeit den Wärmeeintrag deutlich. Das Schutzgas wird dann durch die am Schweißbrenner befindliche Düse in den Schweißprozess eingeleitet, wobei es die Oxidation an der Schweißnaht verhindern soll.
Verwendung
Das WIG-Schweißverfahren unterscheidet sich in seiner Anwendung nach wie vor nach seiner Stromquelle, d.h. Gleichstrom und Wechselstrom. Das Gleichstrom-Schweißen wird zum Schweißen von Stählen aller Art, Nichteisenmetallen und deren Legierungen eingesetzt. Im Gegensatz dazu wird das Wechselstromschweißen hauptsächlich zum Schweißen von Leichtmetallen wie Aluminium und Magnesium eingesetzt. Günstige und hochwertige WIG-Schweißgeräte finden Sie hier: